Understanding ergonomics and pain in the workplace
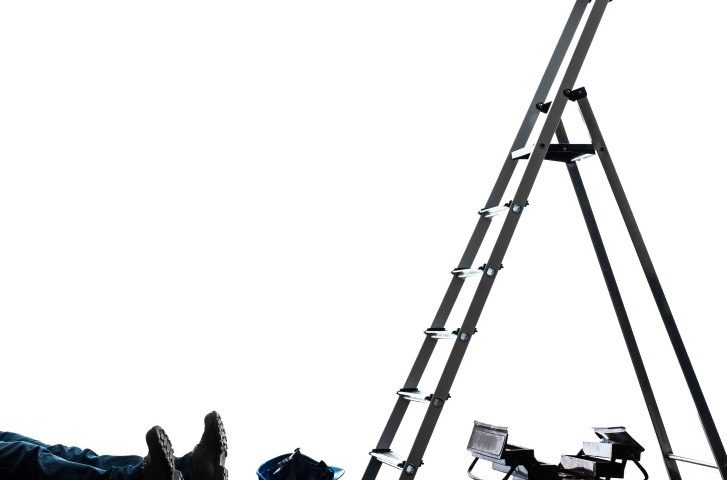
As of April 2019, municipalities across Ontario will be undergoing review and inspections from ministry ergonomists. Recently, the Ministry of Labour implemented – with the goal of being proactive – a municipal health and safety initiative focusing on early identification and prevention of musculoskeletal disorder (MSD) risks in the workplace.
The ministry launched Phase One in April 2018, introducing initiative outreach meetings, information webinars, etc., with a focus on compliance, support, and prevention education. Phase Two began on April 1, 2019, and is set to operate from April 2019 to March 2020.
At the 2019 Ontario Municipal Human Resources Association (OMHRA) Spring Workshop in Niagara Falls, Brian McInnes, Provincial Ergonomist for the Ministry of Labour, addressed questions about Phase Two of the initiative. In addition, Patricia Clausen, Public Service Health and Safety Association (PSHSA) Director, provided tools and resources municipalities can use to develop an MSD prevention program. For more information on developing and implementing a workplace MSD prevention program, visit Preventing pain in the workplace.
Ministry of Labour Workplace Ergonomics and MSD Risk Inspections
Phase Two of the ministry’s health and safety initiative, with ongoing support from PSHSA, is separated into two steps. Step One is the administrative review, an internal responsibility system (IRS) specifically related to ergonomics. Step Two is a physical inspection of the public works department.
McInnes said the ministry is currently looking at visiting 100 municipalities. Since not all municipalities are going to be visited, participants will be selected based on their risk-based ranking – their history for MSDs and lost-time injuries (LTIs). A ministry ergonomist will contact each municipality to identify a date to perform the review, ensuring a worker and management representative, as well as required information and documentation, will be present for the inspection.
Preparation for Workplace Inspections
Noting that a more detailed administrative review may occur if an occupational health and safety inspector is with the ergonomist, McInnes suggested municipalities to be prepared with the following documentation.
Policy and program
Employees are required to develop a written Occupational Health and Safety Policy as well as a program to implement said policy.
Proof of information, instruction, and supervision
Information, instruction, and supervision on MSDs or other ergonomics-related training (e.g., MSD hazards at the job, signs and symptoms, early reporting of symptoms, requirements for reporting MSD hazards/concerns, using a ladder, visibility hazards, etc.) is to be provided.
Joint Health and Safety Committee (JHSC) meetings
MSD hazards, if present, should be discussed during meetings and actions need to be taken to address those hazards. Inspectors will be checking the minutes for discussion around MSD hazards, reports, and solutions.
Workplace inspections
MSD hazards should be looked for during workplace inspections.
Accident investigations
When a worker is disabled from performing their usual, everyday tasks, there needs to be a discussion on what steps should be taken to prevent recurrence. Controls should be evaluated for effectiveness and notices should be provided.
Injury statistics
MSDs should be tracked and areas of priority should be established from jobs or departments with higher MSD occurrences. Rates of occurrences should be determined.
The Ins and Outs of the Physical Workplace Inspection
The physical inspection of the public works department may include observing workers carrying out tasks, discussing tasks with workers, and conducting assessments of MSD hazards. If MSD hazards are observed during the inspection, the ministry ergonomist can perform an ergonomics assessment to determine if there is overexposure to MSD risk – or require the employer to perform an ergonomics assessment themselves. If more than one inspection is being done, McInnes said ergonomists have the option to make future “pop in” inspections.
The following are examples of various hazards ergonomists will be on the watch for during their inspections.
- MSD Hazards: high forces, awkward postures, and repetition (e.g., manual materials handling, assembling/disassembling/constructing, maintenance, etc.); vibration; and contact stress
- Visibility Hazards: required high-visibility safety apparel; plans for preventing being struck by or coming into contact with dangerous objects/substances; and appropriate lighting.
- Fall Hazards: proper usage of ladders; heights and depths that items are stored at and the equipment used to obtain them; and how items are stored based on their weights.
For more information on ergonomics in the workplace, the Ministry of Labour has a database of ergonomics resources that can be found at https://www.ontario.ca/page/ergonomics-workplace. MW
Cassidy Meath is Assistant Editor for Municipal World. After receiving their graduate certificate in Publishing: Book, Magazine, Electronic from Centennial College, Cass gained experience in editing, proofreading, and fact checking through their work with John Wiley & Sons and tbk Creative.
Related resource materials: